External Leakage
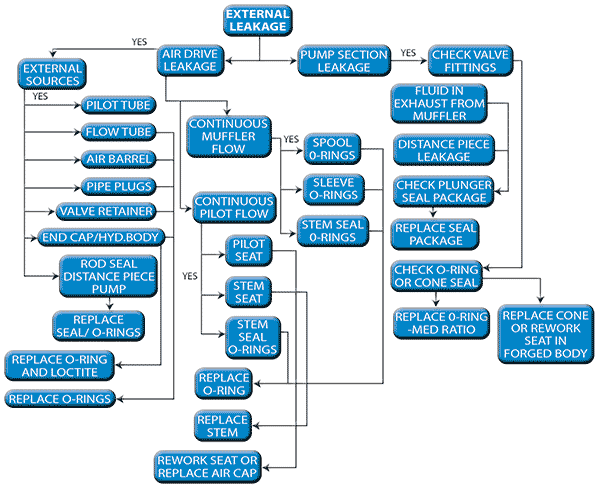
EXTERNAL LEAKAGE:
External leakage is always the result of a defective seal, and can be from the air drive (air or gas leakage), or the pumping section (gas only) leakage. This can cause operational, as well as corrosive and toxic problems, depending on the gas being boosted. In general, external leakage of pumped gas is unacceptable, and must be corrected. External leakage of the air drive may be symptomatic of a condition that could result in a later problem. If the booster is to be driven by "sour gas", then it can be a toxic hazard. In that application, all normal vent ports are piped together and routed to a safe disposal area.
AIR DRIVE LEAKAGE:
Air drive leakage can be detected by the use of "bubble soap" or audible noise if the leak is large enough. "Cyclic" venting through the mufflers and pilot vent port is a "normal" condition for a "standard" booster, and is not a concern unless it becomes "continuous". For boosters with the "severe service cycling modification", there will be some continuous venting from the mufflers, since the PTFE air piston seal does not seal as well as the "O" ring. The following sequence should be used to determine the location of the leakage.
1. If leakage is audible, it is most likely large enough to be located by "feel" of the air flow coming from the leak. If there is no "audible" leakage, then bubble soap should be used, carefully, for locating the suspected leak point. The possible areas to check include:
a. Pilot tube "O" rings
b. Flow tube "O" rings
c. Air barrel "O" rings (at end caps)
d. Pipe plug (1/2 inch) on lower cap sealing pilot chamber.
e. Valve retainer at exhaust end of cycling valve.
f. Connection of gas pumping section to air drive valve end cap. For "distance piece" pumps, leakage out of the rod seal or body seal of the distance piece.
g. Continual flow (in addition to the normal cyclic flow from the mufflers) can be caused by spool "O" ring damage, Sleeve "O" ring damage, or air drive piston "O" ring leakage, and will require some dis-assembly to determine the exact cause.
h. Continual flow (in addition to the normal cyclic flow) from the pilot vent port on the upper cap can be caused by pilot seat damage in the upper cap, damage to the pilot stem molded rubber insert, leakage of the stem seal "O" ring, or contamination on the seating surface.
GAS SECTION LEAKAGE:
Gas section leakage is normally easy to detect. It can be due to the static external seals on the gas end cap, or the dynamic piston/plunger seal. If it is the static seals, a bubble soap check of the joints where the seals are located will show the leaking area. If it is the dynamic "rod" seal, then the leakage can be detected at the rod seal "drain" port between the air drive and gas section. If it is the Piston seal, then the leakage can be detected at the vent port above the gas barrel (this port normally has a plastic "breather" installed to prevent entrance of particulate that could damage seals and surface finishes). In either condition, the defective seal package should be replaced, after it has been determined that there is no damage to the sealing surfaces. Also, visually inspect to determine if externally induced contamination from the pumped gas could have damaged the seal.
See flow chart for a quick overview of all trouble-shooting sequences.